Morgan Rushworth Nitrogen Generators
A nitrogen generator is a device designed to produce high-purity nitrogen gas on demand, directly from the air. These generators work by extracting nitrogen from compressed air through a process known as Pressure Swing Adsorption (PSA) or membrane separation. The resulting nitrogen gas can be used in various industrial applications, including laser cutting, food packaging, electronics manufacturing, and chemical processing.
By producing nitrogen in-house, businesses can reduce reliance on gas cylinder deliveries, lower operational costs, and ensure a continuous supply of nitrogen. Nitrogen generators are highly efficient, cost-effective, and can be customised to meet specific purity requirements and flow rates. Compact and easy to install, they offer a reliable and sustainable solution for industries that require a steady supply of nitrogen. Whether for preserving product quality or enhancing production efficiency, a nitrogen generator is a valuable asset in any modern industrial setup.
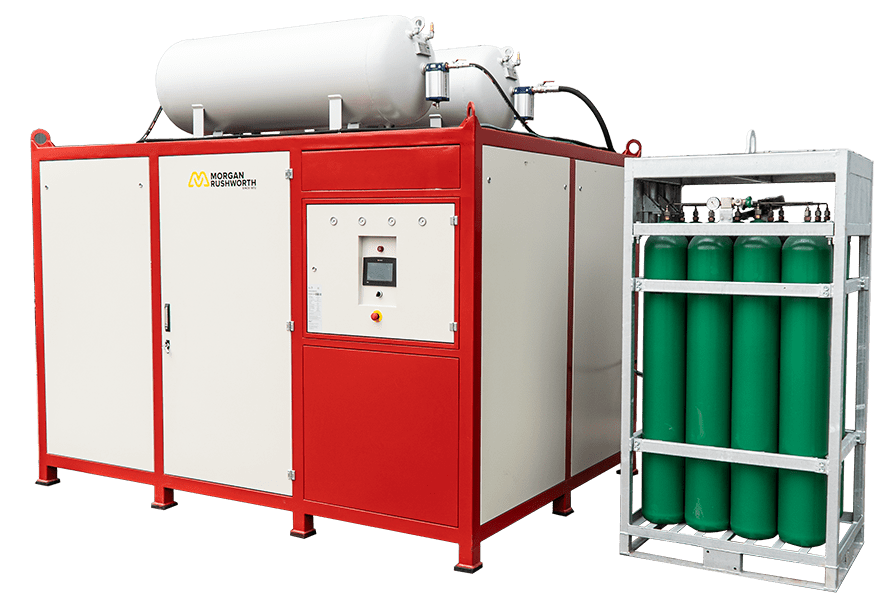
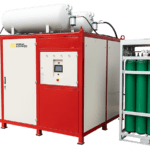
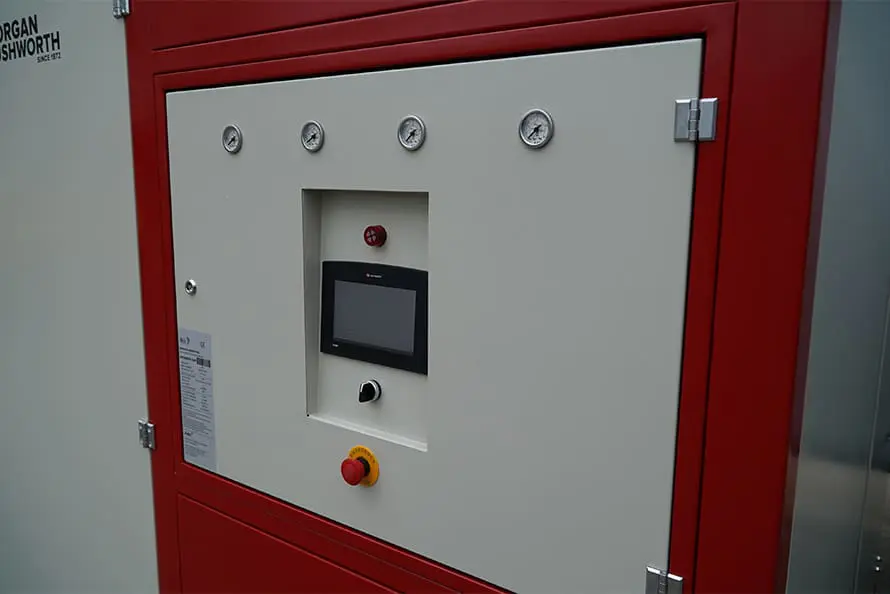
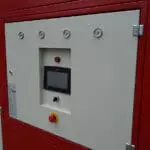
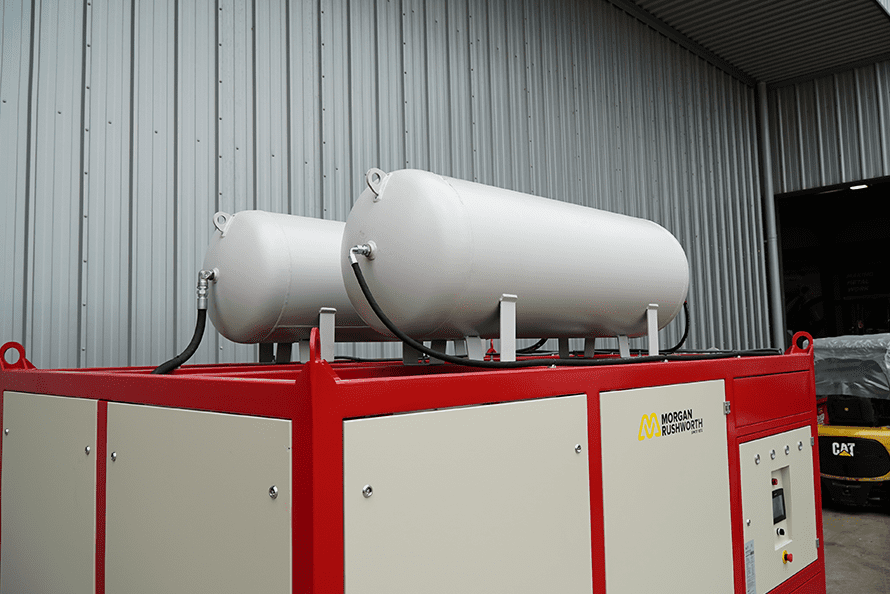
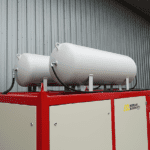
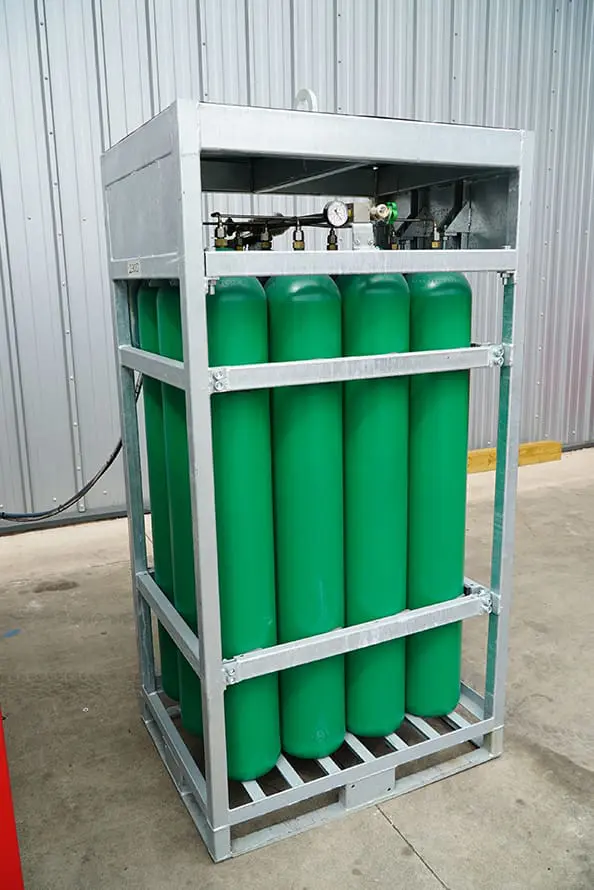
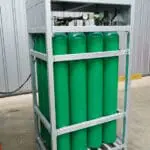
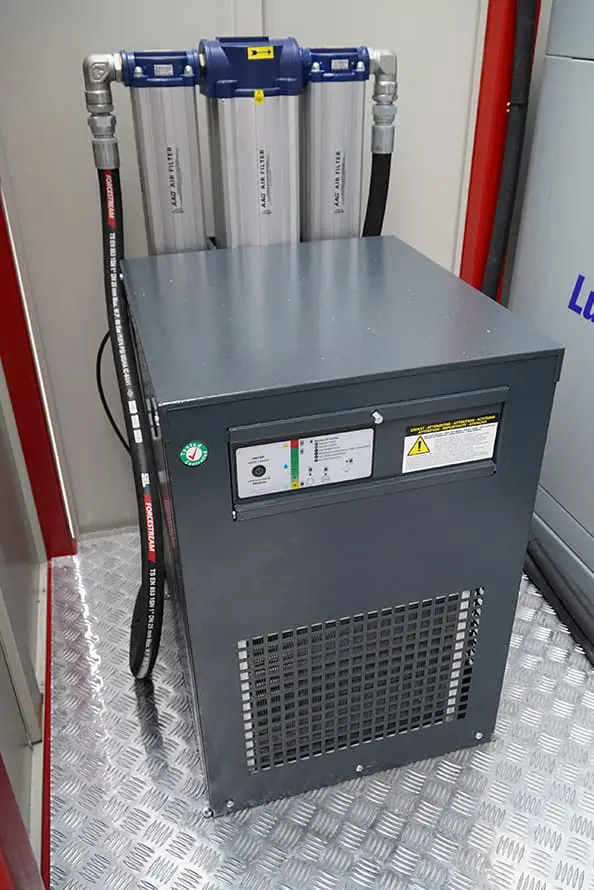
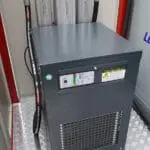
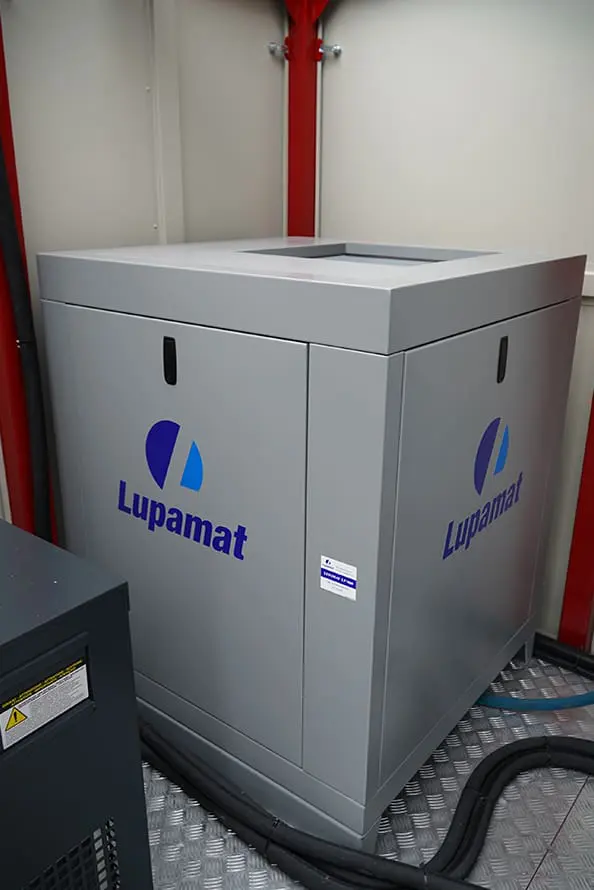
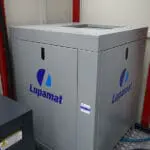
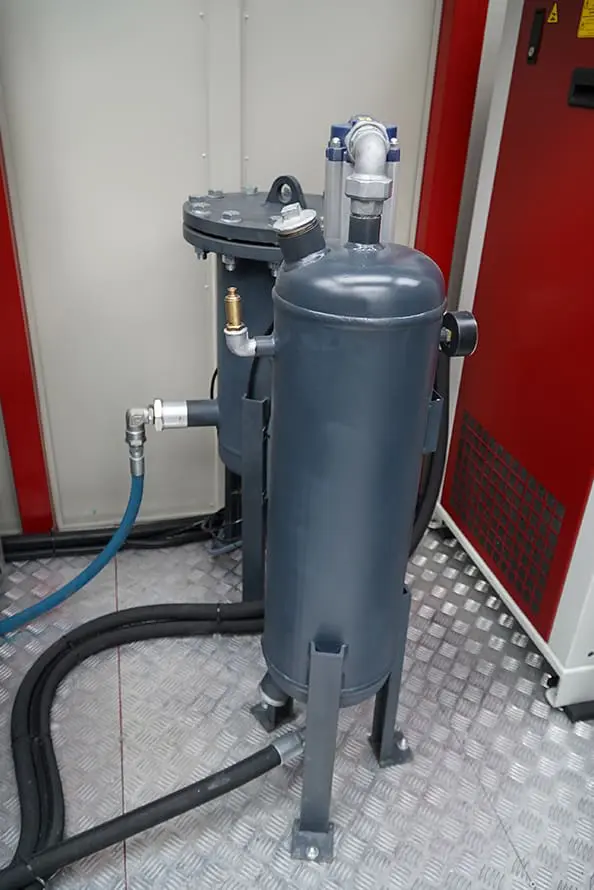
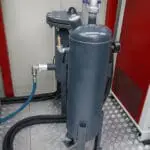
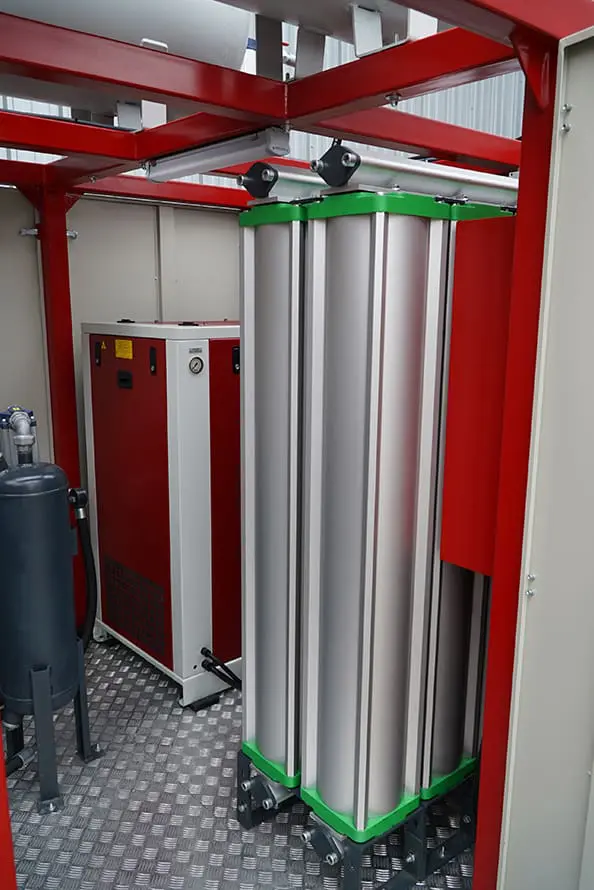
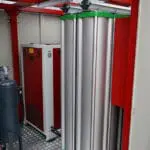
Model | 213 | 226 | 239 | 252 | 265 | 278 | 291 | 304 | 305 | 307 | 309 | 311 | 313 | 315 | 317 | 319 | 321 | |
Servo Speed (In free working condition) | µm | 0.01 | 0.01 | 0.01 | 0.01 | 0.01 | 0.01 | 0.01 | 0.01 | 0.01 | 0.01 | 0.01 | 0.01 | 0.01 | 0.01 | 0.01 | 0.01 | 0.01 |
Coil Thickness (Min / Max) | Bar | 7.5 | 7.5 | 7.5 | 7.5 | 7.5 | 7.5 | 7.5 | 7.5 | 7.5 | 7.5 | 7.5 | 7.5 | 7.5 | 7.5 | 7.5 | 7.5 | 7.5 |
Setting Width Range (Min / Max) | Bar | 6 | 6 | 6 | 6 | 6 | 6 | 6 | 6 | 6 | 6 | 6 | 6 | 6 | 6 | 6 | 6 | 6 |
Power | V | 110-230 | 110-230 | 110-230 | 110-230 | 110-230 | 110-230 | 110-230 | 110-230 | 110-230 | 110-230 | 110-230 | 110-230 | 110-230 | 110-230 | 110-230 | 110-230 | 110-230 |
ph | 1 | 1 | 1 | 1 | 1 | 1 | 1 | 1 | 1 | 1 | 1 | 1 | 1 | 1 | 1 | 1 | 1 | |
Hz | 50-60 | 50-60 | 50-60 | 50-60 | 50-60 | 50-60 | 50-60 | 50-60 | 50-60 | 50-60 | 50-60 | 50-60 | 50-60 | 50-60 | 50-60 | 50-60 | 50-60 | |
99Minimum N2 Flow (Nm3/h) with compressed Air Inlet – Operating Pressure – Up to 11.5 Bar (Standard 7 Bar) | 95% | 155 | 310 | 465 | 620 | 775 | 930 | 1,085 | 1240 | 1,395 | 1,550 | 1,705 | 1,860 | 2,015 | 2,170 | 2,325 | 2,480 | 2,635 |
97% | 103 | 206 | 309 | 412 | 515 | 618 | 721 | 824 | 927 | 1,030 | 1,133 | 1,236 | 1,339 | 1,442 | 1,545 | 1,648 | 1,751 | |
98% | 89.1 | 178.2 | 267.3 | 356.4 | 445.5 | 534.6 | 623.7 | 712.8 | 801.9 | 891 | 980.1 | 1,069.2 | 1,158.3 | 1,274.4 | 1,336.5 | 1,425.6 | 1,514.7 | |
99% | 70.3 | 140.6 | 210.9 | 281.2 | 351.5 | 421.8 | 492.1 | 562.4 | 632.7 | 703 | 773.3 | 843.6 | 913.9 | 984.2 | 1,054.5 | 1,124.8 | 1,195.1 | |
99.5% | 58.4 | 116.8 | 175.2 | 233.6 | 292 | 350.4 | 408.8 | 467.2 | 525.6 | 584 | 642.4 | 700.8 | 759.2 | 817.6 | 876 | 934.4 | 992.8 | |
99.9% | 39.6 | 79.2 | 118.8 | 158.4 | 198 | 237.6 | 277.2 | 316.8 | 356.4 | 396 | 435.6 | 475.2 | 514.8 | 554.4 | 594 | 633.6 | 673.2 | |
99.95% | 32.7 | 65.4 | 98.1 | 130.8 | 163.5 | 196.2 | 228.9 | 261.6 | 294.3 | 327 | 359.7 | 392.4 | 425.1 | 457.8 | 490.5 | 523.2 | 555.9 | |
99.99% | 19.8 | 39.6 | 59.4 | 79.2 | 99 | 118.8 | 138.6 | 158.4 | 178.2 | 198 | 217.8 | 237.6 | 257.4 | 277.2 | 297 | 316.8 | 336.6 | |
99.995% | 16.8 | 33.6 | 50.4 | 67.2 | 84 | 100.8 | 117.6 | 134.4 | 151.2 | 168 | 184.8 | 201.6 | 218.4 | 235.2 | 252 | 268.8 | 285.6 | |
99.999% | 13 | 26 | 39 | 52 | 65 | 78 | 91 | 104 | 117 | 130 | 143 | 156 | 169 | 182 | 195 | 208 | 221 | |
Length | mm | 750 | 800 | 900 | 1,000 | 1,000 | 1,000 | 1,000 | 1,200 | 2,245 | 2,375 | 2,370 | 2,370 | 2,370 | 2,370 | 2,400 | 2,590 | 2,590 |
Width | mm | 750 | 1,060 | 1,270 | 1,400 | 1,600 | 1,800 | 1,900 | 2,000 | 4,074 | 4,024 | 4,020 | 4,020 | 4,120 | 4,120 | 4,125 | 4,200 | 4,200 |
Height | mm | 2,500 | 2,500 | 2,500 | 2,500 | 2,500 | 2,500 | 3,000 | 3,000 | 2,787 | 3,054 | 3,317 | 3,317 | 3,350 | 3,350 | 3,611 | 3,900 | 3,900 |
Weight | kg | 740 | 950 | 1,850 | 2,000 | 2,150 | 2,600 | 3,200 | 3,600 | 4,000 | 4,400 | 4,800 | 5,200 | 5,600 | 6,000 | 6,400 | 6,800 | 7,200 |
Features
- Water separator for inlet of feed pressure air, 1 unit
- Water discharge system with zero air loss, 1 unit (Zeromat)
- Line filters for feeding pressurized air, 2 units (0,5 and 0,01 mg/m3)
- Outlet filter, 1 pc, 0.01 mg/m3
- Pneumatic valves
- PLC control system with fully automated operations
- Pressure switch for automated Idle-Mode
- Sensor for compressed air inlet
- Exhaust mufflers
- Regulator for nitrogen pressure
- Nitrogen Purity Up to 99.999%
- Nitrogen Pressure up to 300 bar (g) (With Nitrogen Booster Compressor)
- Min. Air Pressure 6 Bar
- Max. Particle Consumption – 0.01µm
Options
- 40 Bar Nitrogen Booster
A Game-Changer for Fibre Laser Cutting
Fibre laser cutting has become a cornerstone of modern manufacturing, offering unmatched precision, speed, and efficiency in cutting metals and other materials. However, achieving optimal results depends heavily on the quality and availability of assist gases like nitrogen. Nitrogen acts as a shielding gas during laser cutting, preventing oxidation, improving edge quality, and enabling precise, clean cuts. To ensure a reliable and cost-effective supply of high-purity nitrogen, many businesses are turning to nitrogen generators as a strategic investment.
How Nitrogen Generators Work in Fibre Laser Cutting
Nitrogen generators are designed to produce high-purity nitrogen gas on demand, directly from the surrounding air. These systems rely on two main technologies:
- Pressure Swing Adsorption (PSA): PSA generators use a carbon molecular sieve (CMS) to separate nitrogen from other gases in compressed air. The process yields nitrogen with purities as high as 99.999%, making it ideal for the precision demands of fibre laser cutting.
- Membrane Separation: Membrane-based systems utilise hollow fibre membranes to separate nitrogen from oxygen and moisture. These are well-suited for applications requiring moderate nitrogen purity, offering a compact and low-maintenance solution.
Both technologies ensure a consistent supply of nitrogen, tailored to meet the flow rate and purity demands of fibre laser cutting systems.
The Role of Nitrogen in Fibre Laser Cutting
Nitrogen plays a critical role in the fibre laser cutting process, particularly when cutting stainless steel, aluminium, and other non-ferrous metals. Here’s why it’s indispensable:
- Oxidation Prevention: Nitrogen acts as a shielding gas, displacing oxygen from the cutting zone. This prevents oxidation and ensures a clean, shiny edge, free from discoloration.
- Improved Edge Quality: The use of high-purity nitrogen results in smoother and more precise cuts, reducing the need for post-processing and saving time.
- Enhanced Cutting Speed: Nitrogen allows for faster cutting speeds in certain materials, improving overall productivity.
- Versatility: With nitrogen, fibre lasers can achieve superior results across a wide range of materials and thicknesses.
Benefits of On-Site Nitrogen Generation for Fibre Lasers
Installing a nitrogen generator offers a host of advantages for businesses utilising fibre laser cutting systems:
- Cost Savings: Traditional nitrogen supply methods, such as bottled or liquid nitrogen deliveries, involve significant recurring costs for transportation, storage, and handling. On-site nitrogen generation eliminates these expenses, leading to substantial long-term savings.
- Uninterrupted Supply: Relying on external gas suppliers can result in downtime during delays or shortages. A nitrogen generator ensures a continuous, on-demand supply, allowing uninterrupted laser cutting operations.
- Customisable Purity and Flow Rates: Fibre laser cutting often requires nitrogen with high purity levels. Nitrogen generators can be tailored to meet specific purity requirements and flow rates, ensuring optimal performance.
- Improved Profitability: By reducing reliance on bottled nitrogen, businesses can lower their cost per part. This cost efficiency enhances overall profitability and competitiveness.
- Compact and Scalable: Nitrogen generators are available in various sizes and configurations, making them suitable for businesses of all scales. Whether you’re a small shop or a large manufacturing facility, there’s a nitrogen generator to meet your needs.
- Enhanced Safety: Handling high-pressure nitrogen cylinders poses risks, including leaks and accidents during transport. With an on-site generator, nitrogen is produced at the point of use, minimising these hazards.
Maximising Efficiency with Nitrogen Generators
Fibre laser cutting is all about precision and efficiency. An on-site nitrogen generator not only supports these objectives but enhances them. By providing a steady supply of high-purity nitrogen, it allows operators to focus on production without worrying about gas shortages or fluctuating supply costs. Additionally, the elimination of delivery logistics simplifies operations and reduces the environmental impact associated with transporting bottled gas.
The Bottom Line
For businesses utilising fibre laser cutting, investing in a nitrogen generator is a strategic move that delivers measurable benefits. From reducing operational costs to improving cutting quality and efficiency, nitrogen generators empower manufacturers to achieve their production goals with greater ease and reliability.
By ensuring a continuous supply of high-purity nitrogen, nitrogen generators are not just a convenience—they’re a critical tool for maximising the potential of modern fibre laser cutting systems.