Metal Working fluids can pose a serious risk of harm to your employees’ health, and leave you open to prosecution, if poorly managed. By taking a series of precautions you can minimise the health risks to your employees, and the risk of prosecution to you as the employer.
The risks of MWF lies in its potential to release harmful lung-infecting organisms without being noticed. A welder, grinder or plasma cutter can exhume visible fumes, sparks, and vapours, but not metal working fluids. They stay swirling around in a sump, looking like a mixture of cream and weak coffee, do an essential job without complaining, don’t burn the fingers when handled, and offer up that old-fashioned odour, the tell-tale identity of a skilled hardworking engineer, even outside of the black country.
Fluid systems that contain water or water-mixes can become highly contaminated with harmful bacteria. The bacterial contamination of fluids and associated machinery and pipework should be monitored and controlled.
So how can metalworking fluids so seriously affect us?
- Irritation of the skin or dermatitis.
- Lung diseases, such as occupational asthma, occupational hypersensitivity pneumonitis, bronchitis, irritation of the upper respiratory tract and other breathing difficulties.
How is this harm potentially caused?
- Inhalation of mist or splash particles.
- Skin contact during the preparation or draining of fluids, handling of workpieces, especially through cuts and abrasions or other broken skin.
- Through the mouth if we do not wash our hands before eating.
Unfortunately, what follows, possibly even when an employee has already moved to other duties or left, is an illness or life changing injury. That pursued can culminate in an enquiry under the PUWER (Provision and use of work equipment Regulations 1998), and prosecution.
That is why the Health and Safety Executive, the HSE, has not only devoted a raft of guidance notices specifically on that subject, but why their factory inspectors regularly home in on what to the average worker seems unimportant. HSE inspectors are currently visiting businesses across Great Britain, checking that all risk assessments and mitigations are in place.
So, what is the method of dealing with these risks?
Firstly, prevention and preparation are both crucial. As outlined in the UKLA’s Good Practice Guide. Control measures should be introduced for anyone involved in the provision or use of metalworking fluids, these could include protective gloves, instruments and devices to minimise skin contact (such as splash guards), as well as providing facilities for regular cleaning of exposed skin, especially before breaks or after exposure.
Furthermore, ensuring to use metal working fluids as per the manufacturer’s instructions. Over-diluting fluids can be hazardous, allowing bacterial growth to flourish, or under-diluting fluids can increase the risk of corrosion or skin conditions when exposed – following the recommendations is important for these reasons.
Exposure to metal working fluid mists is a further hazard, so suitable practices should be observed to minimise exposure, be it using LEVs (Local Exhaust Ventilation) or enclosing machines while in operation.
Alternatively, testing of the coolants and fluids can be conducted. It is not a one-off fix, it is a process of management of just FIVE steps which follows the path below:
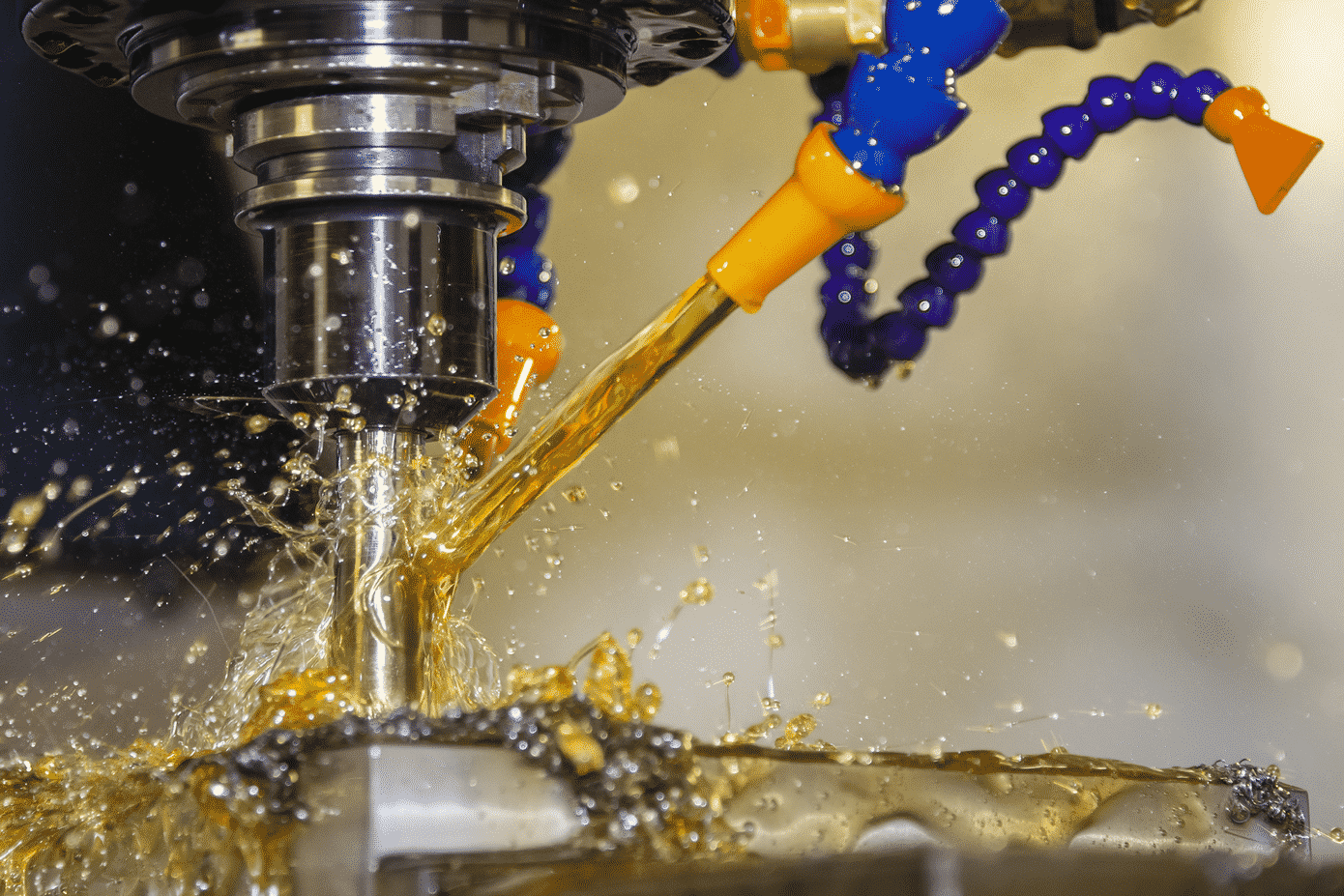
Consider using an external specialist
1 – Conduct a Risk Assessment
An employer must consider the likelihood of a hazardous event occurring, and the consequence. Documented, it indicates that action is being taken to control the risk, which will be to monitor the fluid condition.
If using a specialist, they can supply the initial test kit
2 – Purchase monitoring equipment
Monitoring is a constant process of management and needs to be delegated to a responsible person, either in H and S, or the machine operator.
The test kit includes record sheets which can be copied for multiple machines
3 – Take samples from each machine
These tests can be recorded instantly:
- Temperature
- Visual / Refractometer
- pH
- Tramp
Nutrient needs 24-48 hours to incubate.
Yeasts need up to 120 hours to incubate.
4 – Grow the samples in the incubator
These tests must be grown in the incubator
- cfu/cm² Nutrients
- cfu/cm² Yeast
- Moulds
5 – Record the results
No
MWF Condition under control?
Yes
Treat with biocide or clean out with a suitable system cleaner and refill
Repeat steps 3 – 5
If using an external specialist, it is goods practice to request an annual check visit under PUWER.
Enter a frequency of repeat on the Risk Assessment
There is no specified frequency.
Base it on your usage, extend it if clean conditions prevail, shorten it if poor results repeat.
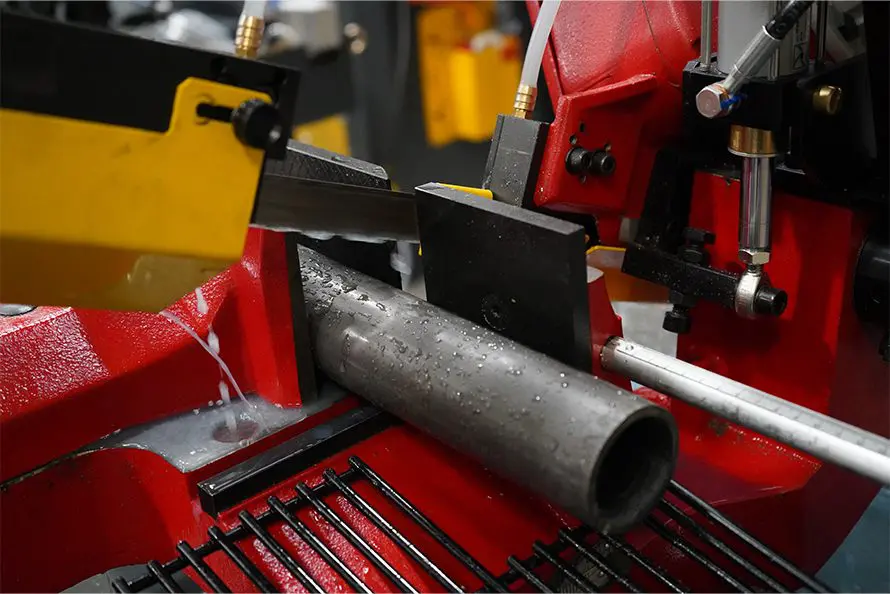
Best practice and solutions from Selmach.
As part of our GoldCut range, Selmach offers three chemical products to assist with bacterial contamination control.
GoldCut 310 Cutting Fluid – A modern biostable semi-synthetic metalworking fluid suitable for all general machining operations on ferrous materials and high carbon steels. Mixed 1 – 8, this fluid helps keep blades cool during sawing, prolonging the life of the blade, and keeps bacterial contamination to a minimum.
GoldCut 314 Gold Spraymist Coolant – Oil used on spraymist coolant systems on saws etc. A highly treated neat cutting oil with low viscosity extreme pressure treatment assists good tool life and a cleaner working environment.
GoldCut BC Biocure – This high performance Biocure is for use in any aqueous solutions and emulsions, such as waterbed Plasmas, and coolant sumps for saws and drills. Extremely potent, it just needs to be added at a concentration of 0.1% to keep bacteria at bay.
GoldCut SC System Cleaner – A professional system cleaner which can be used to flush out your current contaminated coolant sump mixture ready for new coolant.
Check out our safety data sheets on these products here.
Article last updated January 28th 2025.
Published 25th November 2021