Fibre Laser or CO2 Laser? Which cuts fastest? We evaluate the differences, pros and cons between these two laser cutting technologies to help you decide which one to buy for your needs.
Fibre Laser vs CO2 – What’s the difference between the two?
A common question asked is what is the difference between a fibre Laser and a CO2 Laser. The main key differences between the two is the wavelength of the laser, and the delivery method of the laser.
Both machines can engrave and mark a wide range of materials. However, fibre lasers are specifically designed for metal processing, whereas CO₂ lasers are compatible with a broader variety of materials.
Laser cutting technology offers numerous advantages over traditional cutting methods, including precise computer-controlled programming, non-contact cutting, and minimal cutting forces, ensuring cleaner and more efficient results.
Either option provides precise CNC capabilities, accuracy and repeatability.
Wavelengths
Fibre lasers are typically operating on a wavelength of 1,060 nm, whereas CO2 lasers are usually in the 10,600 nm range. This difference affects what materials the laser beam can cut or engrave. CO2 lasers are more suited to organic materials, such as wood, cardboard, textiles etc.
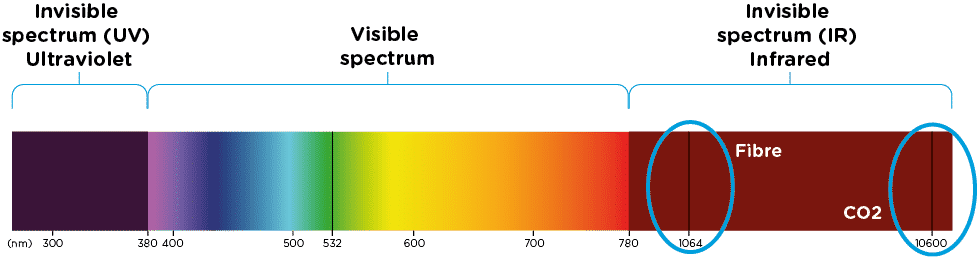
The shorter wavelength of a fibre laser makes it far better suited for cutting metals, as it allows more of the beam’s energy to be absorbed into the material, reducing reflection and increasing efficiency. This makes fibre lasers ideal for sheet metal cutting, including mild steel, stainless steel, and highly reflective metals like copper, brass, and aluminium—materials that CO₂ lasers struggle with or cannot cut at all.
CO₂ lasers cannot cut copper or brass, and while they can cut aluminium, there is a major drawback—a large portion of the beam reflects back into the laser’s optic components, significantly reducing the lifespan of consumable parts and increasing maintenance costs.
A key factor influencing kerf width (the width of the cut) is the laser’s spot size. A smaller spot size increases cutting accuracy and optical density (the laser power per unit area). Compared to fibre lasers, CO₂ lasers typically have spot sizes up to 90% larger, which means they are less precise for fine metal cutting.
However, CO₂ lasers excel in versatility, being capable of cutting a much wider range of materials beyond metals, including plastics, rubber, melamine, leather, cloth, and cork—materials that fibre lasers cannot process.
Fibre lasers also offer zoom and non-zoom cutting head options. Zoom heads allow for adjustable focus spot diameters, giving greater control over kerf width and enabling the cutting of thicker materials at the same power level. In contrast, CO₂ lasers require different heads and lenses to modify spot sizes for various applications.
Click the button below to see a detailed breakdown of what the two technologies can do.
Differences in Beam Delivery
The other way in which they differ, is the actual technology involved in delivering the laser to the material. CO2 tube lasers pass electricity through a CO2 filled tube to create the light of the laser beam, one end of the tube is a fully reflective mirror and lenses to concentrate and reflect the beam through a translucent mirror the other end. Further mirrors and lens are used to bounce the laser down to the material where the heat vaporises the material with intense heat.
Fibre Lasers, as the name implies, utilise a fibre optic cable instead. The laser beam is generated in a similar way, but is directed through a fibre optic cable, eliminating the need for reflective mirrors and lenses until it gets to the cutting torch, making for a far more focused and powerful beam. As a result, Fiber Lasers can be much more powerful than their CO2 counterparts.
IPG Photonics, one of our partners here at Selmach, were the inventors of Fibre Optic Laser technology. They came up with the process and have refined it over the last 30 years, and now offer a broad range of applications, including Laser Cutting and Laser Welding. They’ve been joined by countless other manufacturers now who have developed their own Fiber Laser technology, including nLIGHT, Max Photonics, Raycus and many more.
Investment Costs
As with any new technology, fibre lasers were initially quite a bit more expensive than their CO2 counterparts. However, as the technology has developed, the costs have decreased. Fibre lasers are now practically on a par in terms of purchase cost. More importantly, the ongoing costs of a CO2 laser makes fibre more cost-effective in the long run too.
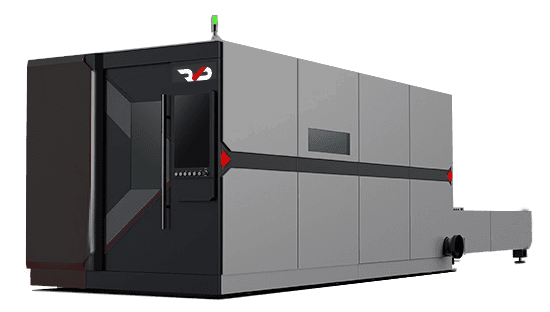
With an increasing number of Chinese and Far-Eastern built machines on the market, these costs have reduced considerably for entry-level machinery, and you can now pick up a Fibre Laser machine for the comparative cost of a high-end Plasma Cutter.
If you’re looking for an entry-level laser machine, to begin your profiling journey – check out our RVD range
Alternatively, if you’re looking for a proper workhorse that will be running flat-out, or for further automation solutions – check out our Morgan Rushworth Range
Speed
Fibre lasers are ideal for cutting thin gauge material quickly, whereas CO2 is a lot slower in comparison. The difference in wavelengths means that the spot size of the fibre laser is up to 90% smaller than CO2. Because the material will absorb more of the beam’s energy (rather than reflect it), fibre lasers can cut faster and more precisely than their CO2 counterparts.
On thin gauge, fibre is twice or even three times as fast as a comparative CO2 laser would be. With faster cutting you can increase your workload capacity, and keep your employees working efficiently too. The obvious benefit of this is that the faster you can cut material, the cheaper the per-item cost of your cut pieces.
Thicker materials are generally faster too with a fibre laser. CO2 lasers often need to do a second pass to complete a cut through thick steel. The assist gas from the CO2 laser becomes trapped, creating a bubble around the cutting head.
The final time saving aspect of a fibre laser is they are ready to go instantly. There is no warm-up time due to the technology in use. CO2 lasers typically take 10-20 minutes to be operational.
Maintenance
CO2 works by reflecting the laser beam to the cutting surface with a mixture of mirrors and gases. The mirrors on a CO2 laser are extremely sensitive and highly vulnerable to dirt/dust particles meaning they are easily destroyed and often need replacing. Each time this occurs it comes at a hefty cost of several thousand pounds to the customer. Mirror and lens cleaning, beam realignment and ongoing maintenance are all needed on CO2 lasers. Whereas with fibre, there is simply a fibre optic cable routing the laser to the cutting surface. This heavily reduces maintenance, and subsequently costs.
Less maintenance and downtime means more efficiency and cost savings.
Ongoing cost savings
CO2 lasers use up a lot of energy to keep them running. Fibre is far more energy efficient than a CO2 laser, typically 2-3 times more efficient, drastically cutting down your energy consumption. CO2 lasers also utilise helium gas, which is becoming increasingly more expensive.
Fibre laser also has the advantage of not required ceramic marking compound to be applied for engraving, further reducing the costs both in terms of consumable materials and time spent applying it.
Swapping a CO2 to a fibre laser will therefore reduce your energy, and gas consumption. This will further reduce your per/part costs, and is also more environmentally friendly too.
Below is an example of how the machines can compare in terms of energy costs.
Technology | Target Working Time / Year | Duty Cycle (Laser On) | Average Power Consumption | Power Consumption / Year |
---|---|---|---|---|
CO₂ Machine (6kW) | 3,500 h | 70% | 65 kW | 158,900 kWh |
Fibre Machine (6kW) | 3,500 h | 70% | 22 kW | 53,900 kWh |
Power Savings / Year | 105,000 kWh |
Physical Size
Fibre lasers take up less physical space than their CO2 equivalents, a highly underrated benefit. A smaller machine frees up workshop space. Extra space allows staff to move around more easily, or more space for storing material.
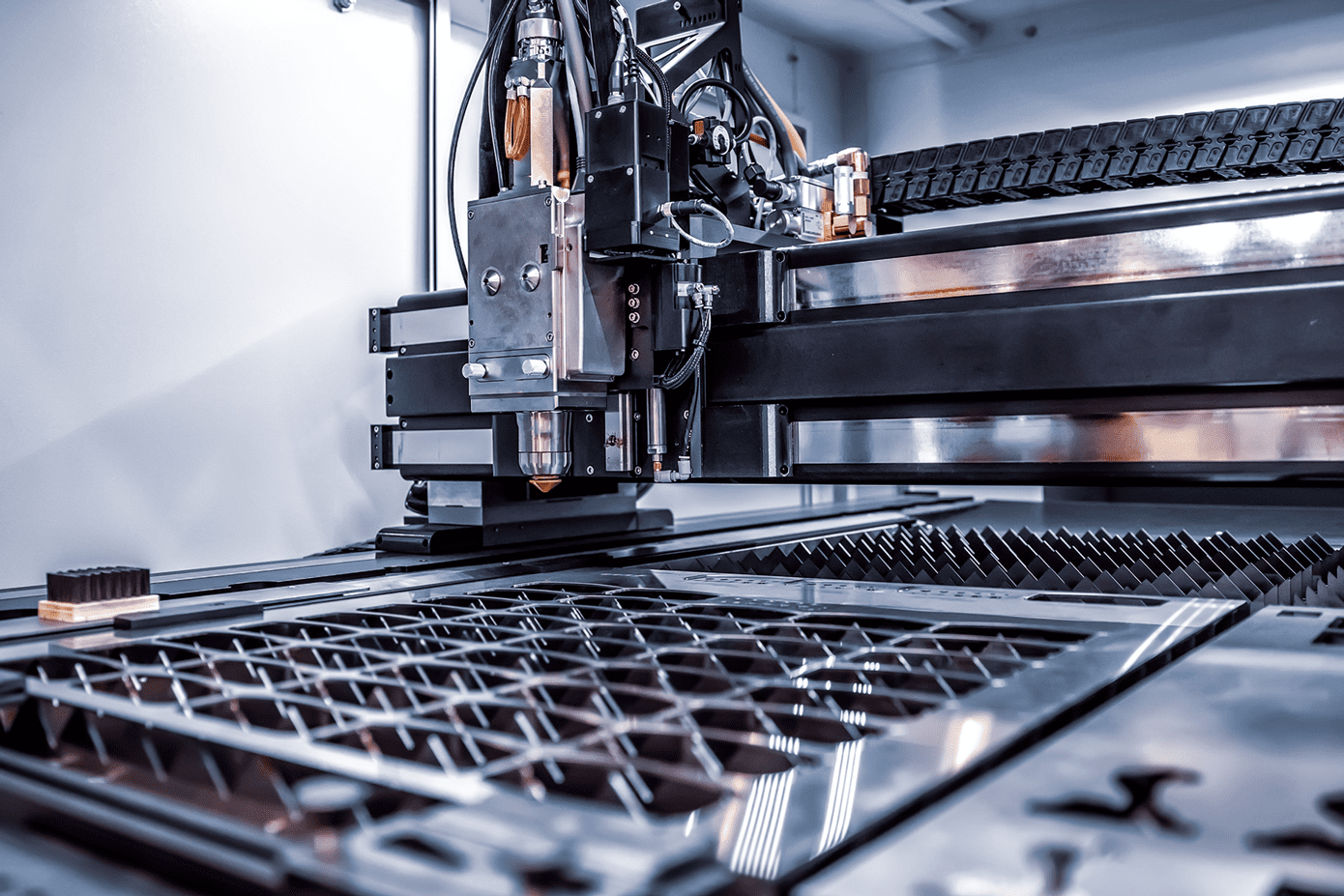
It could even allow you to further improve efficiencies by bringing in additional equipment. Typically, the cross-sectional area of a CO2 laser being approximately 3 or even 4 times larger than the equivalent fibre laser.
Ultimately, the best laser cutter for you depends on your operational needs.
If your focus is on engraving and cutting non-metallic materials such as acrylic, wood, card, leather, and fabrics, a CO₂ laser is the ideal choice. These machines are widely used across industries due to their exceptional precision, allowing for intricate engraving—even detailed photographic reproductions.
Many everyday items have been produced or customised using a CO₂ laser, often without you even realising it.
For industrial metal cutting, however, fibre laser cutters are the superior option. Designed for high-powered, heavy-duty applications, fibre lasers provide clean, precise, and highly consistent cuts on metals—something a CO₂ laser simply cannot achieve.
Their ability to handle tougher materials makes them essential in aerospace and automotive manufacturing. Additionally, fibre lasers excel at marking fine details on metals and other surfaces that some CO₂ machines struggle with, ensuring precision for even the most intricate designs.
If you’d like to find out more about the fibre lasers available through Selmach, please visit our CNC Fibre Laser Ranges
Outsourcing your laser cutting? You are likely paying too much. If you haven’t currently got a laser at all, read our post here about how to end laser cutting outsourcing.
Published 2nd February 2025