The concept of laser cutting first became a reality back in the 1970’s and has seen continuous research and development since. Today we have a wealth of laser cutting machines to meet the demands of our industry. But how does a CNC Fibre Laser work?
Fibre Laser is the latest technology, that built on the speed and efficiency of CO2 lasers before it, by decreasing the amount of maintenance required, and reducing the footprint of the machines.
The most versatile machine
Fibre laser machines are seen as some of the most versatile with good reason. They can cut through mild and stainless steel, or aluminium of increasingly higher and higher thicknesses. It has often been said that fibre laser machines are initially expensive and historically there has been some truth in that. However nowadays, the cost of this technology has tumbled, and with machines manufactured in the far East, you can pick up a CNC Fibre Laser machine for well under £100,000. When the claim of “they’re expensive” is weighed against its many benefits, an altogether different perspective emerges.
Make savings from day one
For larger scale production, savings are made from day one thanks to cheaper processing and dramatically quicker production times. For smaller scale operations and one-off batches, the benefits of CNC technology allow for quick and easy production at the touch of a screen, with little in the way of tooling costs and operator intervention.
How does a fibre laser work?
The Laser Light Path
Fibre laser is a highly efficient and automated way of cutting but that doesn’t mean it simply switches on and goes mindlessly to work. The path of the laser light is constantly monitored and adjusted as needed. The CNC fibre laser’s lenses and adjustment lenses work with core components to focus correctly alter angles and move the beam – constant and precise automation that its predecessors cannot compete with.
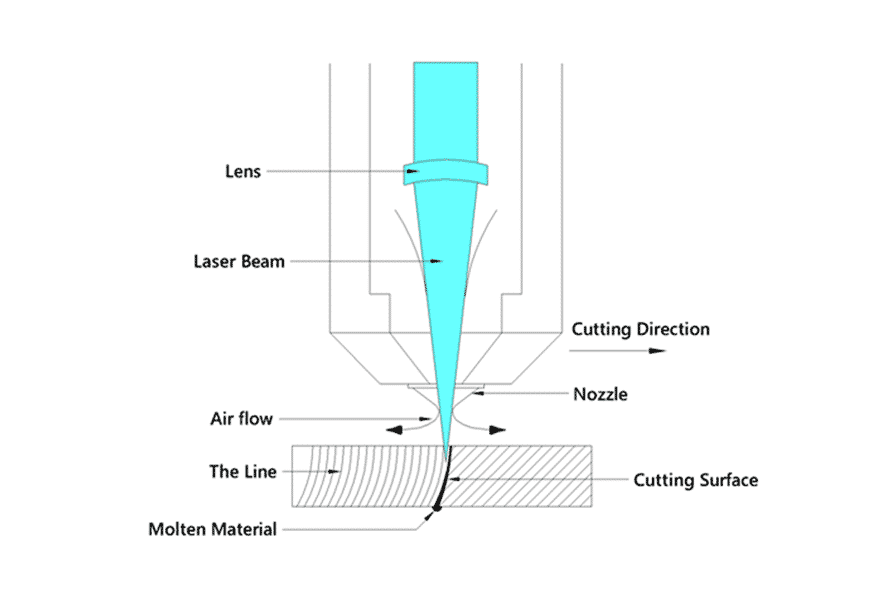
The Laser Generator
The power source for the laser beam is the generator. This, the heart of a CNC fibre laser machine, differs from a CO2 type in that the laser is seeded then amplified within a glass fibre. The resulting beam, with a wavelength of approximately 1 micrometre, can be concentrated into a very small spot (about one hundredth of the minimum size of a CO2 produced laser), making it ideal for cutting reflective materials.
The Fibre Laser Cutting Head
If the laser generator is the machine’s beating heart, you might refer to the laser cutting head as the business end of the CNC fibre laser, yet it is a part of the machine with surprisingly few consumable parts. Since the laser beam is remotely generated and delivered to the head via an optic fibre, expensive lenses and mirrors are out of the way of any potential collisions. It is able to take on a wide range of jobs with little or no need for replacing and reinstalling bespoke toolings or waiting for expensive parts to arrive.
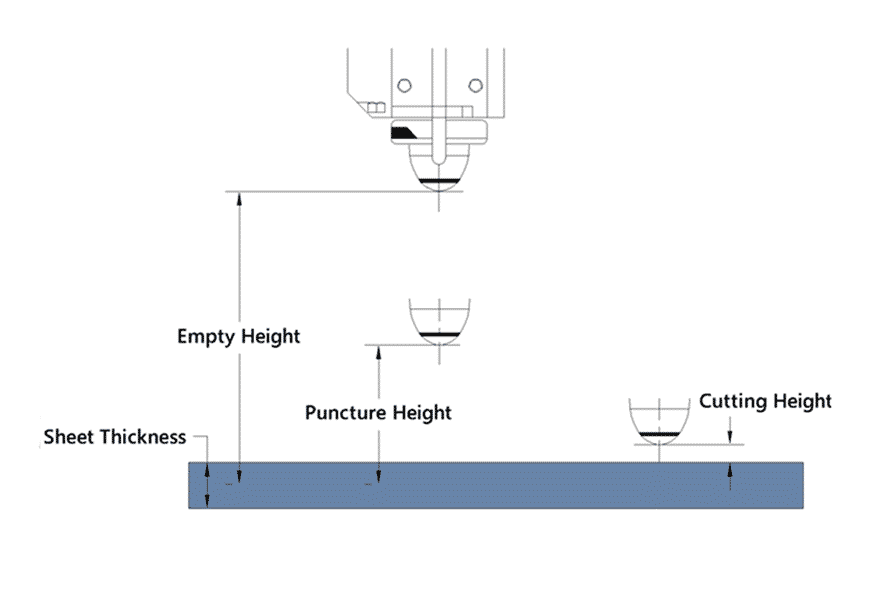
The Focus Position
Few things have greater influence on finish and quality as the focus position of your fibre laser’s nozzle. Different materials naturally require different nozzle heights and a nozzle that is out of focus will not produce the best results.
Few materials however are perfectly even at microscopic scales, meaning the focal length of your laser beam needs constant adjustment. This is where the capacitive sensor comes in, providing constant real time feedback of the distances between nozzle and workpiece to the system’s CNC brain and keeping your laser beam perfectly focused.
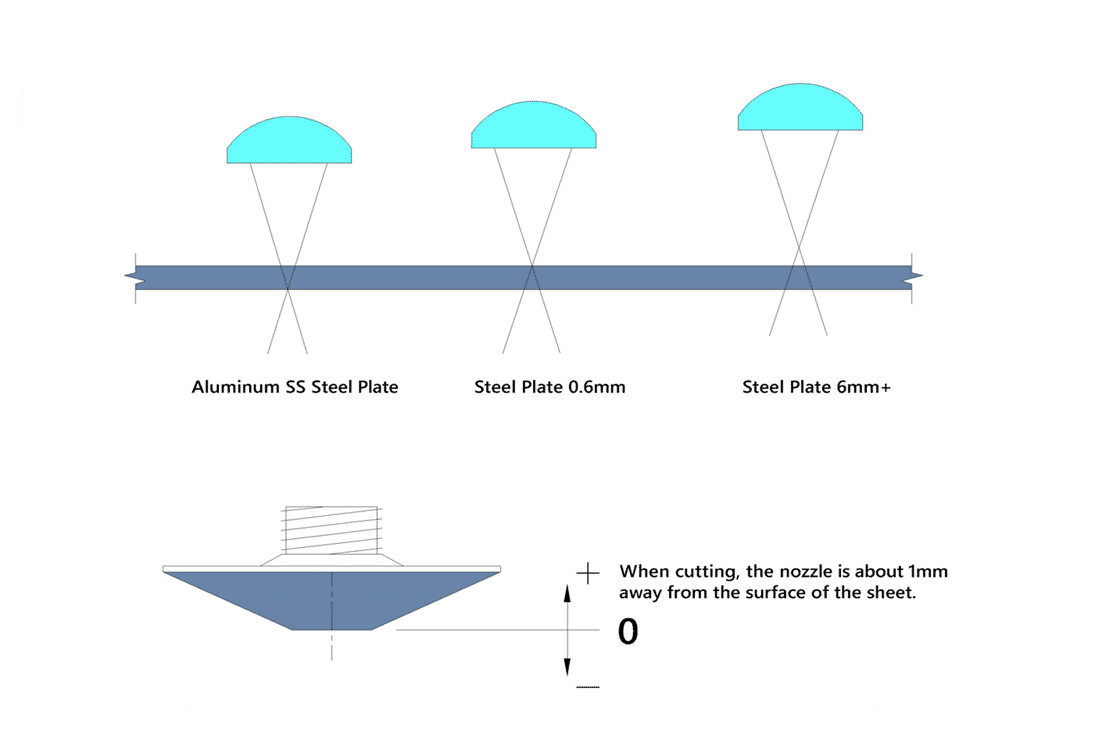
Speed & Power
Speed and power are both important factors in cutting width and quality of cut and the thickness limits of a workpiece. As a general rule of thumb, the more powerful the laser beam then the faster your laser machine will cut and it will be able to handle materials of greater thicknesses.
Balance cutting power against speed
Less than optimal settings and that laser power can result in roughness, burning and an overall decrease in cut quality. CNC/NC software can adjust and balance cutting power against speed automatically to preserve quality and precision.
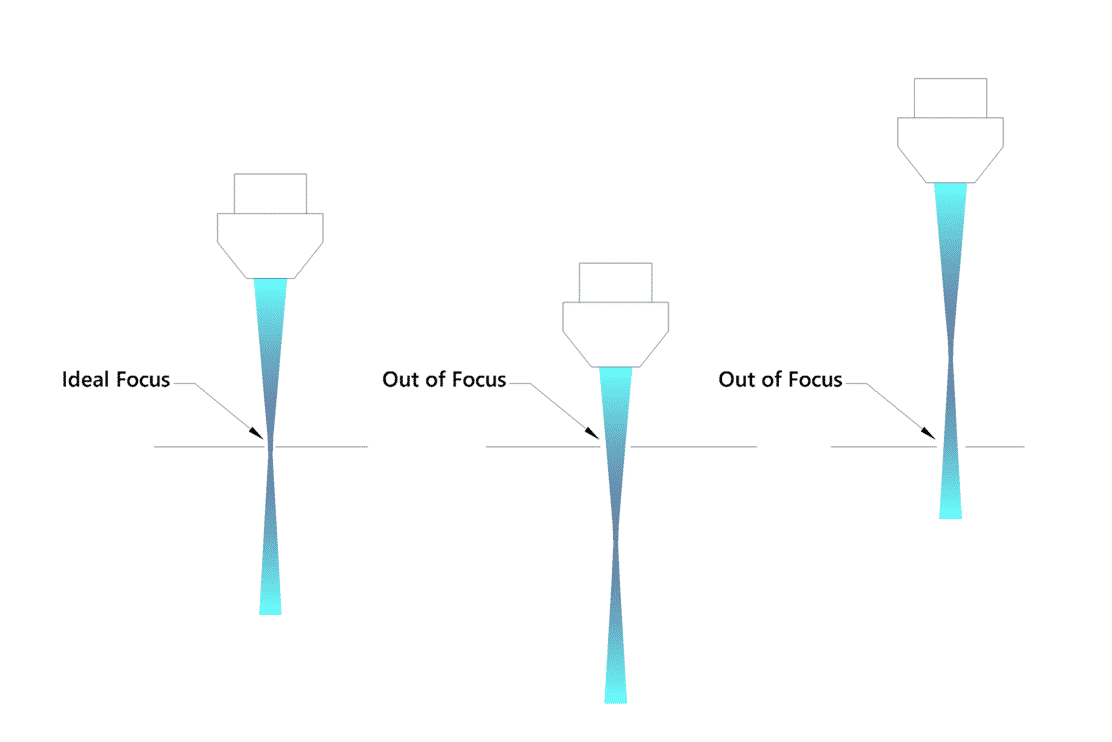
Auxiliary Gases
Gases can affect several different aspects of the fibre laser cutting process with different gasses much better suited to some materials than others. Getting it right is important.
The gases your laser cutter uses serve several purposes, they dispel slag that forms in the cut material’s kerf, they also help to cool the processed material and reduce the temperature of the affected area, in some cases even protecting the base metals themselves. They perform a similar function for the laser machine’s protective lenses, eliminating contamination and overheating. The requirements for each of the above tasks are of course different in terms of flow requirements and pressures.
Selecting your chosen auxiliary gas
The three gases most commonly used are nitrogen, oxygen and air.
Nitrogen tends to be the gas of choice for cutting materials such as aluminium alloys or stainless steel. The thicker plate materials generally require higher pressures to blow off melt and eliminate oxidising effectively.
The purity of oxygen is important to preserve plate cutting quality; if purity is not high then the water and other impurities present in air can cause damage to lenses and inconsistent back and front cutting surfaces.
Reduce cutting costs
Air is very cheap compared to the other gases and even though it contains around a fifth of oxygen, cutting efficiencies are dramatically less than when using purified oxygen. However, some metals and alloys such as aluminium and stainless steel will oxidize from exposure to air, therefore if the quality requirements are high, purified gases may be needed, however, if the final piece is to be painted or processed further then air can be used, reducing costs with a cutting gas that is far more economical.
Selecting your chosen auxiliary gas in line with the characteristics of your materials is vital to attain the quality of end-product you need.
Fibre Lasers are fast, efficient and incredibly versatile, if you’d like to find out more, please contact the sales team.
Published 7th February 2024