LightWELD continues to captivate individuals with its laser welding, showcasing superior aesthetics compared to alternative welding methods. However, the question arises: are these appearances too good to be true?
To address this query, IPG took the initiative to conduct thorough testing. We dispatched samples to Sturbridge Metallurgical Services, Inc., situated in Sturbridge, Massachusetts, for an impartial third-party assessment. Accredited by NADCAP (National Aerospace and Defence Contractors Accreditation Program) and A2LA (American Association for Laboratory Accreditation), SMS possesses the expertise and resources necessary to conduct an independent evaluation of the test samples.
Subjecting laser welds to rigorous examination, IPG referred to the guidelines set by the American Welding Society (AWS) established in 1993. A committee of experts from the aircraft and aerospace industries formulated AWS D17.1:2017, an American National Standard. Focused on Class A, the most demanding category covering critical aerospace applications, our samples underwent testing. Butt joints in plates of 0.036” (~0.89mm), 0.075” (~1.9mm), and 0.120” (~3.05mm) were meticulously produced, adhering to ASTM standard procedures. Sections were prepared using ASTM standard methodology and meticulously inspected at 50X magnification. A total of 26 cross sections underwent scrutiny, revealing no cracking, incomplete fusion, porosity, inclusions, or any other defects. The weld profile passed all assessments, and no instances of underfill were observed.
During the ultimate tensile testing, seven samples underwent evaluation. Remarkably, only one failed at the weld joint, whereas the remaining six failed at the base material. The elongation of the six samples that failed at the base material ranged from 48% to 59%, while the one that failed at the weld joint had an elongation of 54%. Although the sample size is relatively small, all weld samples were deemed acceptable according to AWS D17.1:2017 Class A Standards.
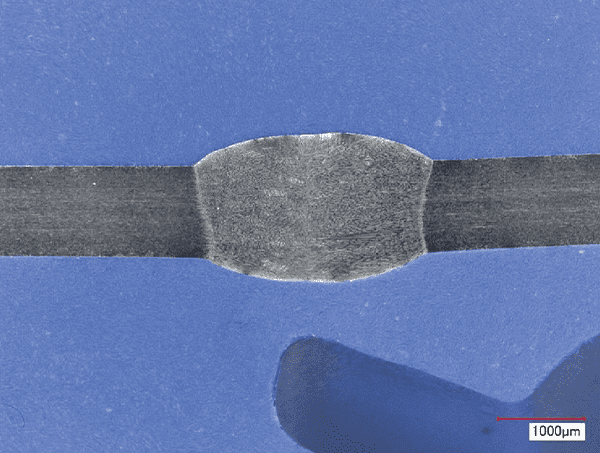
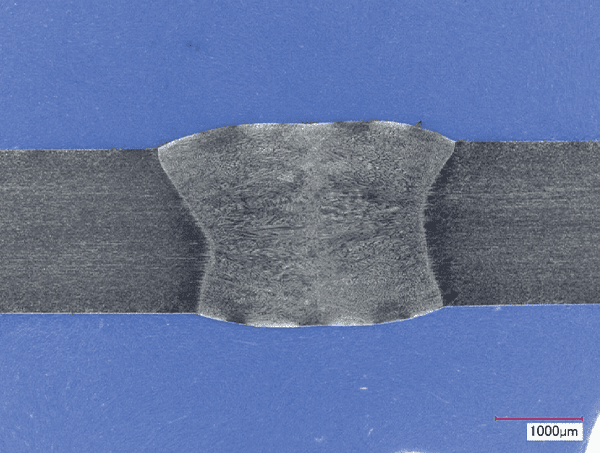

In all instances, no cracking, incomplete fusion, porosity, inclusions, or other defects were detected during weld tests for butt joints in 304 stainless steel plates of 0.036” (~0.89mm), 0.075” (~1.9mm), and 0.120” (~3.05mm). The weld profiles successfully passed all tests, with no observed underfill.
The outcomes of the third-party evaluation conducted by Sturbridge Metallurgical Services affirm that LightWELD consistently delivers welds that conform to stringent industry standards, especially for critical aerospace applications. This underscores its efficiency and quality in welding applications. In summary, LightWELD provides a swifter and more effective welding solution compared to traditional MiG and TiG techniques. Its high power density facilitates deep penetration and faster welding speeds. Moreover, when parts fit together seamlessly, filler wire may be omitted, resulting in an aesthetically pleasing and robust weld.
Using the XR Model, IPG also conducted a test on a 6000 Series Aluminium Ladder. During testing, two samples were evaluated at both the end and middle of the rung.
Each sample was able to withstand a maximum load of 300 kg and ultimately reached a load of 385 in all tests. No visible failure or deformation is formed in the rungs.
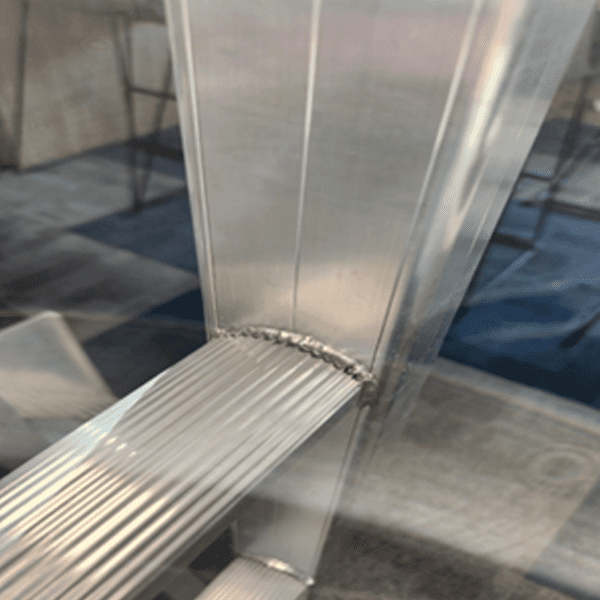
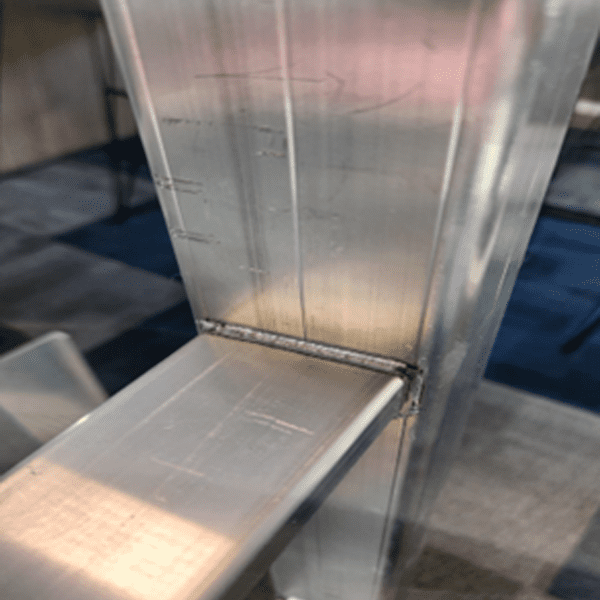
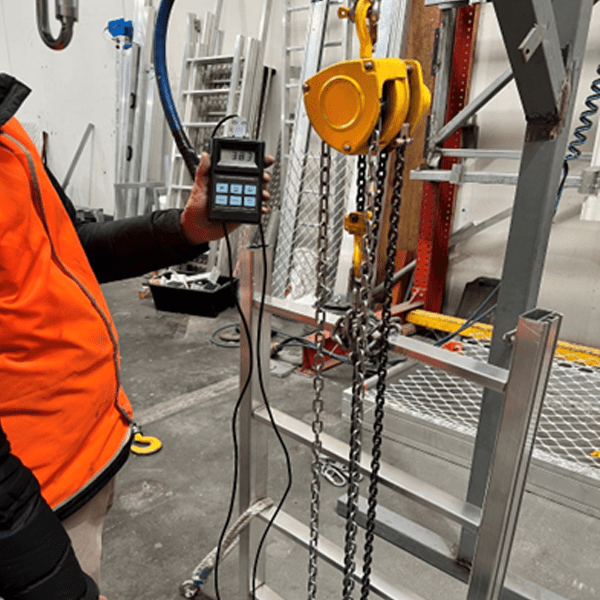
If you’d like to find out more about Laser Welding, you can see the system in action either in our showroom in Hereford, or our mobile demo van can come out to yourselves.
Book a demonstration using the form below!
Published 9th January 2024