Introduction to Section Rolling Machines
Section roller machines are a crucial part of metal fabrication, allowing manufacturers to bend and shape metal sections into precise curves, arcs, and rings. These machines are widely used in industries such as construction, shipbuilding, automotive, and structural engineering to create components that meet exacting specifications.
One common area of confusion in metal rolling relates to Nominal Bore (NB) and Outside Diameter (OD), particularly when working with pipes and tubes (Circular Hollow Sections). In this article, we’ll break down the differences and cover other essential aspects of section rolling.
Understanding Pipe and Tube Rolling
Pipes and tubes are often used interchangeably, but they have distinct characteristics. The key difference lies in their measurement:
- Pipes are typically defined by their Nominal Bore (NB), which refers to the approximate internal diameter.
- Tubes are measured by their Outside Diameter (OD), which is the external dimension of the pipe or tube.
When working with section rolling machines, understanding these differences ensures accurate bending and fitting, preventing issues like misalignment or poor joint connections.
The capacity charts for our machines all deal in Outside Diameters for tubes (Circular Hollow Sections), as for us, that’s the crucial measurement in regards to our machines, and the rollers and dies you’d require.
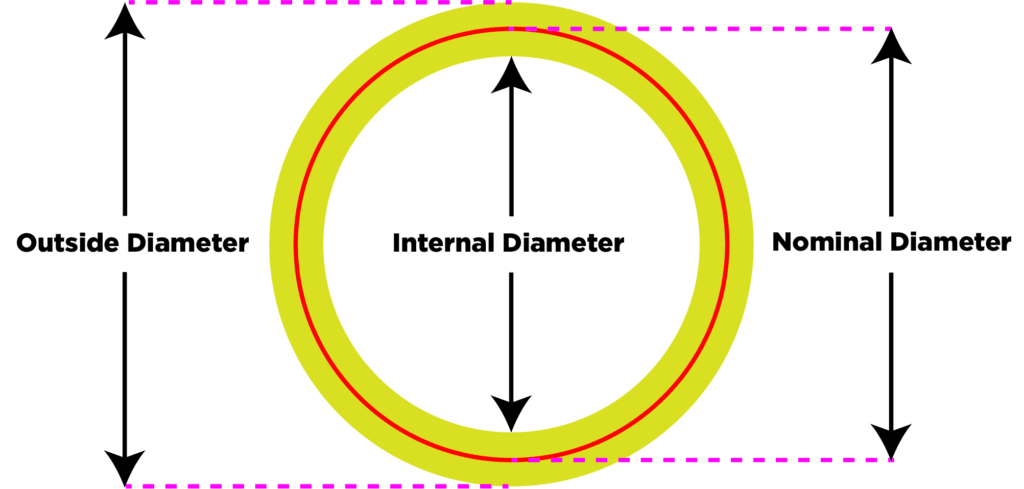
Nominal Bore vs. Outside Diameter: What’s the Difference?
Here’s a quick reference table to illustrate the difference between NB and OD:
Nominal Bore (Metric / NB / DN) | Nominal Bore (Imperial) | Pipe Outside Diameter (Metric) |
---|---|---|
10mm | 3/8″ | 17.2 mm |
15mm | 1/2″ | 21.3 mm |
20mm | 3/4″ | 26.9 mm |
25mm | 1″ | 33.7 mm |
32mm | 1 1/4″ | 42.4 mm |
40mm | 1 1/2″ | 48.3 mm |
50mm | 2″ | 60.3 mm |
65mm | 2 1/2″ | 76.1 mm |
80mm | 3″ | 88.9 mm |
100mm | 4″ | 114.3 mm |
125mm | 5″ | 139.7 mm |
150mm | 6″ | 168.3 mm |
175mm | 7″ | 193.7 mm |
200mm | 8″ | 219.1 mm |
225mm | 9″ | 244.5 mm |
250mm | 10″ | 273.0 mm |
300mm | 12″ | 323.9 mm |
350mm | 14″ | 355.6 mm |
400mm | 16″ | 406.4 mm |
450mm | 18″ | 457.0 mm |
500mm | 20″ | 508.0 mm |
550mm | 22″ | 559.0 mm |
600mm | 24″ | 610.0 mm |
650mm | 26″ | 660.0 mm |
700mm | 28″ | 711.0 mm |
750mm | 30″ | 762.0 mm |
800mm | 32″ | 813.0 mm |
850mm | 34″ | 864.0 mm |
900mm | 36″ | 914.0 mm |
1000mm | 40″ | 1016.0 mm |
As shown in the table above, two pipes with the same Nominal Bore may have different Outside Diameters depending on their schedule (wall thickness). This is important for rolling applications, as the OD determines the rollers and dies required.
Factors Affecting Section Rolling
Rolling pipes and sections isn’t just about bending metal—it requires careful consideration of multiple factors to ensure the best results:
- Material Type – Different metals (e.g., steel, stainless steel, aluminium) respond differently to rolling processes.
- Wall Thickness – Thicker walls require more force and may be prone to flattening during bending.
- Bend Radius – Tight bends require more precision to avoid deformation.
- Spring back Effect – Metals naturally try to return to their original shape after bending, so compensation is needed.
Types of Section Rolling Machines
There are various types of section rolling machines used in fabrication:
- Manual Rolling Machines – Ideal for small-scale or light-duty bending tasks.
- Mechanical & Hydraulic Section Rollers – Powered machines for thicker materials.
- CNC-Controlled Section Rollers – Provide high precision and repeatability for large-scale production.
Here at Selmach, we sell a range of Morgan Rushworth Powered, Hydraulic, and CNC Section Rollers.
Applications of Section Rolling
Section rolling machines are used in a variety of applications, including:
- Structural Fabrication – Bridges, buildings, and steel frameworks.
- Pipework and Handrails – Essential for industrial and architectural projects.
- Automotive and Aerospace Components – Custom-formed tubes and sections.
- Decorative Metalwork – Spiral staircases, railings, and artistic structures.
Common Challenges and Solutions in Rolling
Even with advanced machinery, section rolling comes with challenges. Some of the most common issues include:
- Deformation & Wrinkling – Caused by improper material handling or excessive force.
- Ovality in Pipes – Can be minimised by using the correct roller settings.
- Material Inconsistencies – Different metal grades may require unique rolling techniques.
- Accuracy Issues – CNC machines can help ensure precise bending with minimal deviation.
Choosing the Right Section Rolling Machine
When selecting a section rolling machine, consider the following:
- Material Compatibility – Ensure the machine can handle the metals you work with.
- Capacity – Check the maximum section size and wall thickness it can roll.
- Automation & CNC Capabilities – Useful for improving precision and reducing manual labour.
- Versatility – Machines with adjustable rollers can accommodate various profiles.
Maintenance and Best Practices for Section Rolling Machines
To keep your section rolling machine in optimal condition:
- Regularly inspect and lubricate moving parts.
- Ensure rollers are aligned properly to prevent material distortion.
- Keep dies and tooling clean to reduce wear and tear.
- Train operators on best practices to improve efficiency and accuracy.
Section rolling machines are essential tools in metal fabrication, and understanding the differences between Nominal Bore (NB) and Outside Diameter (OD) is crucial for accurate rolling. By considering factors like material type, bend radius, and machine capabilities, you can achieve precision results and avoid common challenges.
If you’re looking for a high-quality section rolling machine, check out our range of section rolling machines or contact our team for expert advice!
Published 7th March 2025